The aerospace and defense industries are on the upswing again after a hit early in the pandemic, which has resulted in increasing orders for top quality engine and precision parts, structural parts and aeronautical subassemblies. With over $712 billion in revenue reported for the industry in 2021, operating profits are up 136%, according to PwC analysis. And global military expenditures hit an all-time high of $2.1 trillion in 2021, according to the Stockholm International Peace Research Institute.
That means manufacturers and CNC machining centers need to be prepared to meet the challenge.
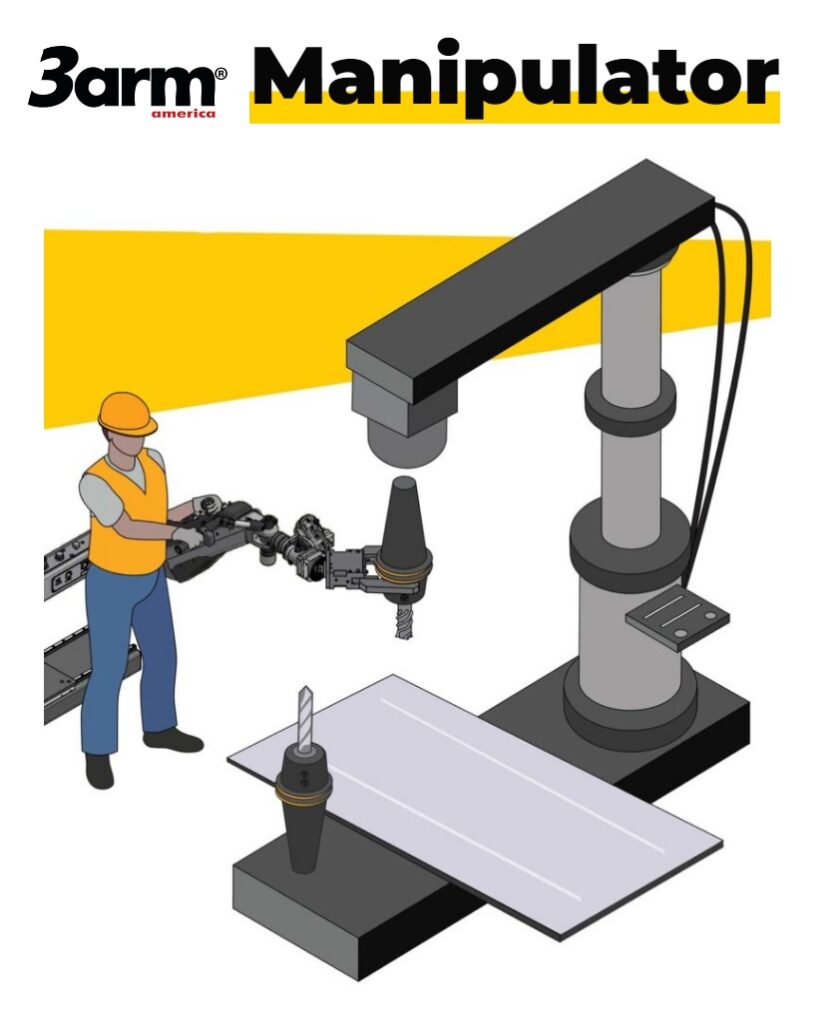
New technologies are accelerating the shift to digital and operational efficiencies, according to the 2022 Aerospace and Defense Industry Outlook by Deloitte US. In fact, Deloitte states that A&D firms that focus on innovation and utilize efficiency- and productivity-enhancing technologies, like lift assist solutions by 3arm America, that accelerate time to market and reduce production times will be better prepared for 2022.
Since technology in the aerospace industry is continually evolving, high quality CNC machining is a critical component of the industry. And engineering teams at high volume CNC machining centers are looking at new technologies to help increase production and quality, while dealing with an increasing shortage of skilled labor.
The extremely high level of precision needed within the aerospace industry requires manufacturers to implement innovative technologies to improve processes. For example, utilizing automated deburring and finishing solutions to meet the required tight tolerances consistently and reliably and lift assist solutions to handle heavy parts and tools for employee safety and retention.
Productivity Challenges for Aerospace and Defense Industry CNC Machining Centers
When the pandemic hit, U.S. aerospace companies let go 57,000 employees. Smaller manufacturers are still struggling to fill job vacancies and, with an industry upturn coming, it’s likely the crunch will only get worse. It’s incredibly challenging to fill highly skilled CNC jobs since precision machinists require apprenticeships and years of specialized training.
So, easing the load for your valuable employees is one way to help with employee safety and retention. Many machining centers are understaffed, which results in overworked and fatigued operators prone to injuries, accidents and lowered productivity. The constant lifting of heavy parts or transferring expensive tool holders in and out of CNC machines can result in costly consequences, such as:
- Damage to expensive parts
- Damage to expensive tool holders
- Repetitive motion injuries for operators
- Operator accidents
- Decreased productivity
- Decreased product quality
- Lost business
In heavy production CNC centers, operators setting up for a new job may strip the magazine of 50-100 tool holders and then load them onto a cart. And some of these tool holders for precision aerospace parts can weigh up to 45 pounds. Many of these tool holders will hold a sharp tool such as an end mill, drill or cutter, and trying to orient it upside down to put the taper into the spindle is dangerous and will leave the operator prone accidents and injuries.
Just changing out tool holders and milling cutters can lead to musculoskeletal disorders due to the repetitive motion lifting heavy weights and the awkward positioning involved affixing the holder in the spindle of a milling machine.
For example, if you’re an aerospace manufacturer that does a significant amount of heavy machining, your operators are probably lifting a 20–pound CAT 50 or HSK 125 tool holder, then adding a milling cutter that weighs around 25 pounds. Then they may add carbide inserts, which are extremely sharp, and insert the tool holder positioned upside down so that the taper can fit into the spindle – an awkward process which requires the operator to contort their body.
The Negative Effect of Workplace Injuries in Aerospace and Defense Industries
Continuing with the previous example, the operator is moving approximately 45 pounds in and out of the CNC machine repeatedly, potentially subjecting themselves to cuts, muscle strains and other injuries. The BLS reports over 50 percent of non-fatal occupational injuries resulting in missed work are caused by musculoskeletal disorders, and the most common areas affected by these injuries are the shoulders, back, hands, knees and ankles.
The cost of workplace injuries to manufacturers can be staggering – just one carpal tunnel claim can cost a company almost $65,000 in direct and indirect expenses and have an effect on the following:
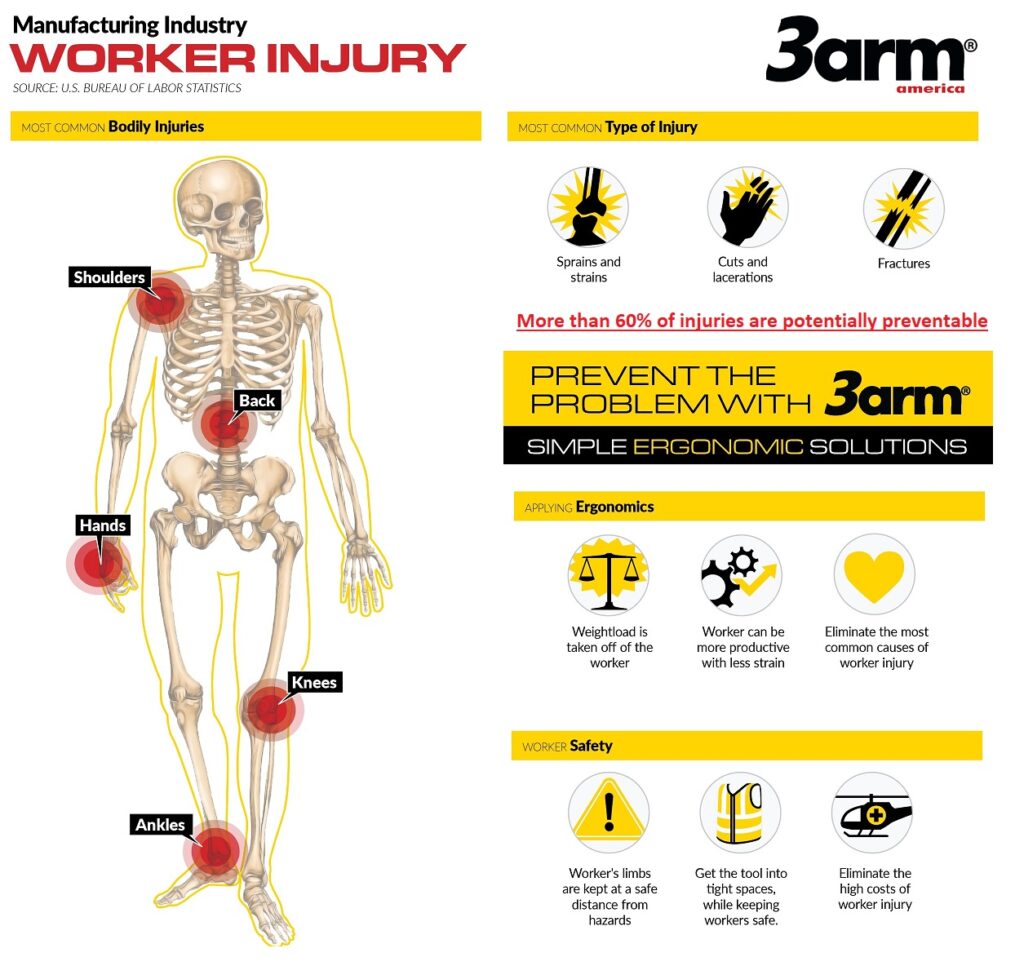
- Reduced safety. Operator fatigue can cause inattention to tool placement or misplacement of tools. This can result in accidents and injuries to employees and damage to expensive tools and the products worked on.
- Long-term injuries. Operators often develop physical injuries over time due to repetitive motions, strain from lifting heavy weight and awkward body contortions to affix tools to tool holders.
- Increased costs. Employee injuries, damaged tools and products, inconsistent quality and inefficient processes result in additional costs and increased scrap and production time.
- Employee turnover. Employees exposed to injuries and safety issues will be forced to retire or leave to find better employment, taking industry knowledge with them.
- Employee recruitment. Prospective employees will take note of the physical demand required and will be more likely to take a position at a company that includes the aid of an ergonomic lift assistance device like 3arm. Having lift assist solutions will also lead to increased diversity in your talent pool.
- Team morale. A job that negatively affects an employee’s health and safety destroys morale. Implementing a 3arm solution demonstrates that employers care for their staff’s health and safety and can boost morale, increasing productivity and job satisfaction.
Benefits of Using a 3arm Manipulator in Machining Centers
One way to significantly reduce negative consequences of this task is to invest in a lift assist solution. 3arm’s M5 Manipulator helps reduce fatigue and strains on the operator by effortless lifting and manipulating tooling for CNC Machines. This 3arm lift assist solution is suitable for any type and size of CNC tool up to 110 pounds.
A 3arm Manipulator can carry the weight of the tools and tool holders, orient and drop the tool holder into a preset at the machining center, and change the end mill, drill, inserts or deburring and finishing brush. Once the offset is determined, the operator can pick the part out of the preset and either put it back into the spindle or magazine of the machine, alleviating the unsafe force exertions of these tasks from the operator.
3arm’s Manipulator is a “pick and place” solution that can be designed with a wide variety of mounting options and accessories to improve ergonomics, reach and mobility. Putting an M5 Manipulator on a custom-built trolley cart offers maximum versatility for machining centers and allows the operators to move and position the arm easily.
Features of the M5 Manipulator – the only arm for pick and place operations:
- Options for gripper jaws, vacuum or magnet attachments
- Custom grippers ensure part will not be damaged when picking up
- Options on a variety of handles
- Optional rotating and/or revolving head assemblies
- Vertical reach of 28” and horizontal reach of 65”
- 110 lb weight capacity
- Can be base- or top-mounted
- Available with or without brakes
- Ideal for indoor industrial settings
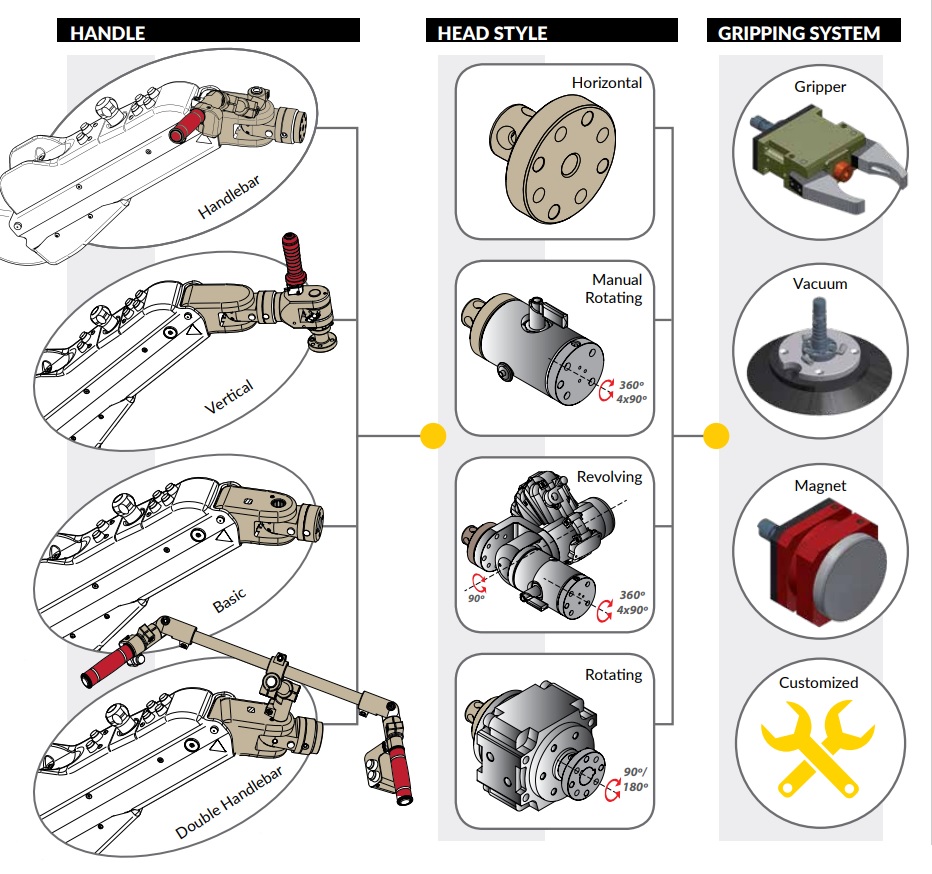
This example of a custom-built Manipulator arm and trolley demonstrates the benefits of a 3arm lift assist solution for high–volume CNC machining centers.
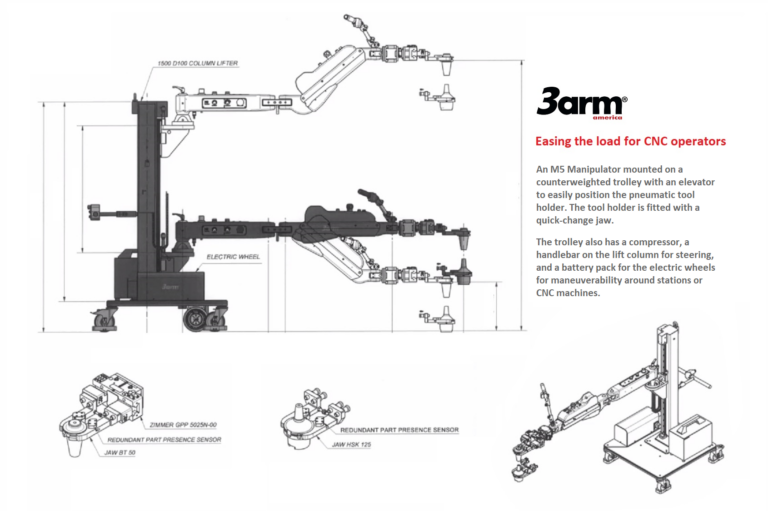
- The manipulator is fitted onto a column mounted on a counterweighted trolley. The column allows flexibility in vertical reach (up to 28 inches) and the counterweights allow differing weight tools to be used on the arm.
- The trolley has a battery pack to power the electric wheels and the handle on the column that drives the trolley as well as raises and lowers the arm on the column.
- The trolley also contains a small compressor to power the pneumatic arm, which can be extended to reach a maximum horizontal reach of 65 inches.
- This Manipulator arm has a handlebar for maneuverability, custom head members for rotation of the tool holder, interchangeable tool holders and quick-change jaw grippers for HSK and CAT 50 and other tool holders.
The M5 Manipulator arm by 3arm is a versatile and easily maneuvered solution for aerospace and defense industry CNC machining centers to protect their most valuable assets: their employees. And in today’s labor market, easily attracting qualified talent and retaining knowledgeable employees is critical. The cost benefits of increasing the health and safety of your staff are significant.
With an increase in productivity and work quality, investing in a 3arm Manipulator for your high-volume, high-precision work is a no brainer. Contact our reps to see how we can design a solution for your needs.