Torque-driving applications are common in manufacturing and other industrial industries. Assemblers, fleet maintenance operators, machining center technicians and others who use power fastening tools can experience a jolt to the wrist when the fastener is completely tightened. The sudden transfer of force is the torque reaction.
These types of fastening tools can cause torque reaction injuries if not used with equipment that can mitigate those forces. Without tools like torque arms to absorb torque reaction, like those offered by 3arm America, repeated exposure to torque reaction and absorption can be brutal for operators.
Handling heavy torque-driving tools and potentially absorbing upwards of 885 ft lbs (1200 Nm) of torque can be hazardous to an operator and it can lead to musculoskeletal disorders, injuries, tool damage, imprecision and inconsistency, and all the workplace costs that come with these concerns.
Fortunately, there are solutions available today that alleviate the strain of using torque-driving tools. Torque arms, such as the wide selection of 3arm tool-holding series arms, render these heavy tools weightless, absorb torque and ensure consistency.
What Does a Torque Arm Do?
What is a torque arm for industrial applications and what does it do? A torque arm is an ergonomic tool-holding arm that can hold torque-driving tools for operators during tightening, bolting, fastening and other applications. By holding the tool, the arm renders it weightless and absorbs the torque reaction.
Manufacturers, fleet maintenance teams and a range of other companies commonly use torque arms to hold tools like pneumatic screwdrivers and drills, impact wrenches and nutrunners for applications like:
- Assembly line work
- Heavy equipment assembly and maintenance
- Automotive underbody work
- Parts and components assembly
- Maintenance of vehicles in transportation, mining, agriculture and construction
The features and capabilities of torque arms vary. For example, at 3arm America, we have several different tool-holding arms with varied torque ratings so our customers can choose the best arm for their application. We also have a broad selection of head members to pair with our torque arms which provide varied ranges of articulation.
>> Check out a demonstration of the impact absorption of the 3arm Series 3 paired with a Nutrunner set to 100nm of torque in this video:
The Series 7 heavy duty tool balancer arm is our most heavy-duty option for a high-torque-reaction arm. This arm can absorb up to 885 ft lbs (1200 Nm) of torque. It can hold and easily handle the heaviest tools like torque wrenches, taking the weight and strain off the operator. It’s perfect for heavy duty fleet vehicle maintenance in industries like construction, earth moving, mining, trucking, farming and more. The Series 7:
- Can hold large, heavy tools (up to 132 lbs)
- Allows for flexible movement due to radial arm which rotates 360 degrees attached to pendulum arm that rotates 180 degrees on both sides.
- Add further range of motion with choice of tool-holding headmembers
- Added reach and mobility with compatible carts, rails and lifts
- Corrosion-proof for use in various environments
- Keep operators’ hands safe from pinch zones
- Fail-safe features such as tool-trigger activated brakes
- Can be fitted with a reaction bar, which reduces tool slipping or turning
The maximum torque rating and tool weight (torque/weight) for each of the series arms is as follows:
Series 0 Single Tilting Arm: 650 Nm (479 ft lb)/77 lbs
Series 1 Dual Tilting Arm: Little to no torque/22 lbs
Series 2 Tilting and Radial Arm: 120 Nm (88 ft lb)/22 lbs
Series 3 Tilting and Radial Arm: 650 Nm (479 ft lb)/77 lbs
Series 4 Dual Tilting Arm: 300 Nm (221 ft lb)/53 lbs
Series 6 Telescoping Arm: 300 Nm (221 ft lb)/40 lbs
Series 7 Heavy Duty Arm: 1200 Nm (885 ft lb)/132 lbs
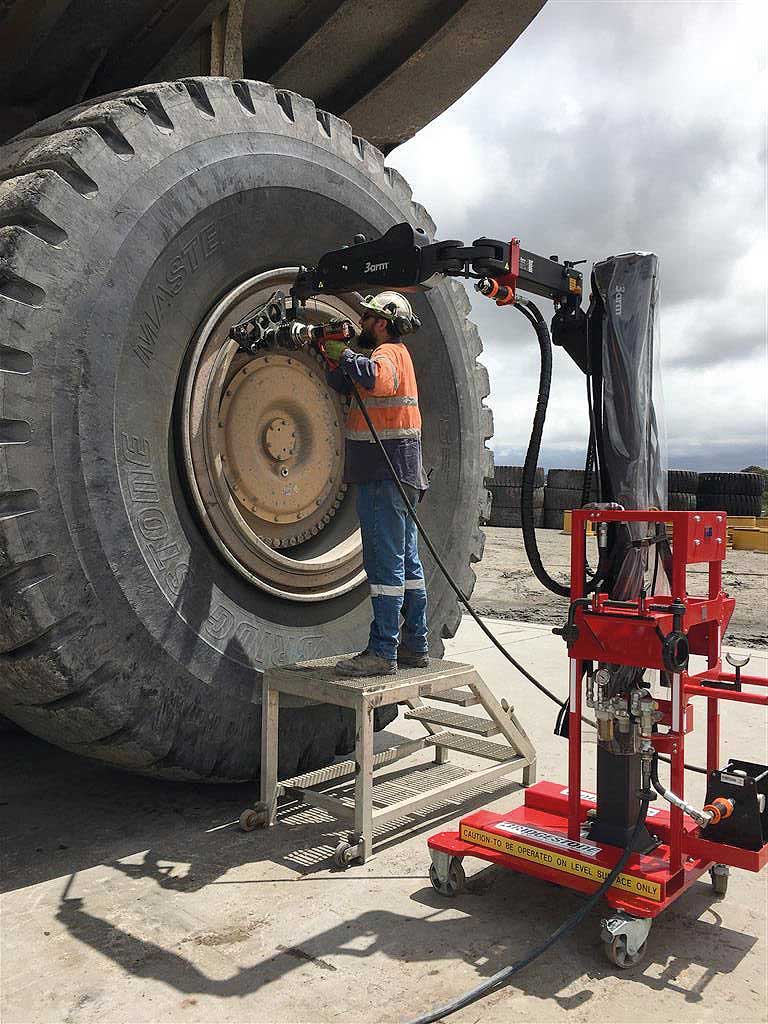
A note on torque arm mounting, head members and accessories
Designing a 3arm solution for your application goes beyond selecting an arm. The maximum torque for each arm also depends on the orientation, head member, length and other factors. For example, see these torque recommendations for the Series 3:

Our experts can calculate a precise torque rating to ensure your requirements will be met/exceeded from the thousands of possible 3arm component combinations. We offer various options for head members to allow for different levels of articulation. And we can work with you to determine the best mounting solutions and accessories if you need mobility, extended reach and/or braking options.
Why Use a Torque Arm?
Using a torque arm for your application has many benefits, including:
- Protecting your employees from the long-term effects of torque on their bodies.
- Reducing the opportunity for injury from torque reaction.
- Taking the weight of heavy tools off your employees to reduce instances of fatigue and strain.
- Improving the overall ergonomics and comfort of workstations to support employee health and well-being.
- Allowing for greater precision and consistency in the application itself.
- Optimizing overall production time by eliminating strenuous work, tool handling and frequent breaks related to strain and fatigue.
- Reducing the chance of damaging or mishandling expensive torque-driving tools.
What Harm Can Come from Not Using a Torque Reaction Arm?
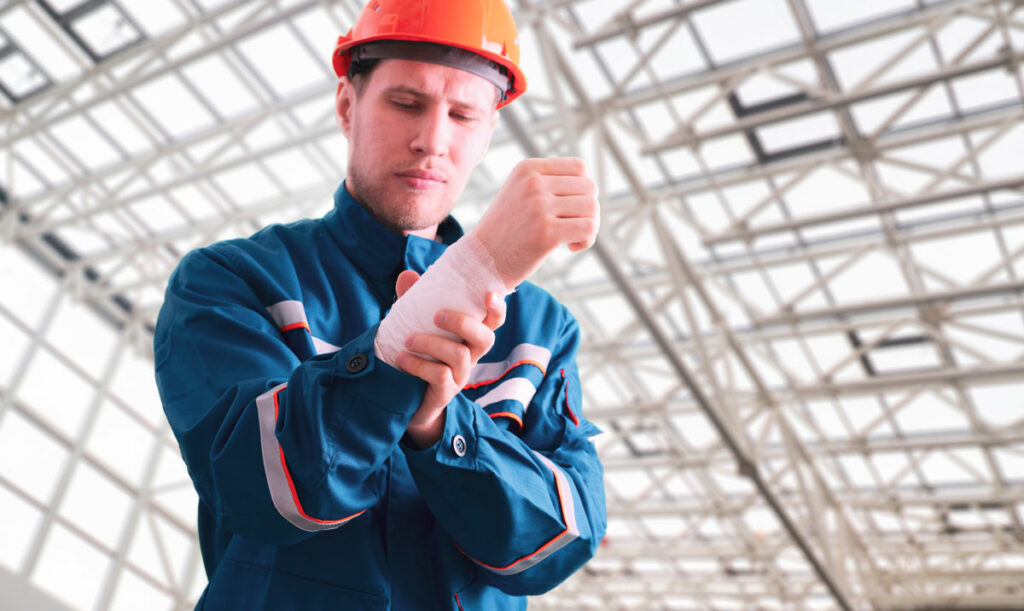
Performing torque-related tasks without the support of a tool-holding arm can affect your people, morale, tools, production rate and quality – all impacting your bottom line.
People: Torque absorption and constant handling of heavy tools can have short- and long-term consequences for operators. In the long-term, they can develop health concerns related to repetitive motions, strain, fatigue and absorption of the torque itself. For instance, they may develop a musculoskeletal disorder like carpal tunnel. Short-term, torque-related injuries can happen in an instant. All it takes is for an operator to hold the trigger a moment too long for the torque to transfer into their arm. Consider the impact if they’re an assembler driving a bolt requiring 50 ft lb torque.
Tools: The price tags on torque-driving tools for industrial applications are nothing to scoff at. They’re typically in the thousands, and once you’ve purchased one you want it to be in commission for as long as possible. However, as expensive as these tools are, they’re also heavy. When they’re handled for long periods of time, particularly in uncomfortable positions, there’s always a chance a fatigued operator can drop the tool. Repeated drops will mean tool repair and could eventually put the tool out of service. Securing the tool in a torque arm will reduce the likelihood of damage.
Learn about three critical production assets you can protect with 3arm. >>
Production Quality: When you’re not using a torque arm, you’re relying on the balance and precision of the operator. While operators are trained professionals and you can put a great deal of confidence in them, it’s difficult to achieve quality and precision efficiently in applications that involve fatigue and possible accidents due to torque reaction and heavy tools.
Recruiting and Retention: Having strenuous torque-driving work that’s not supported by a torque arm can affect your ability to recruit and retain employees. They likely have other job opportunities with less arduous conditions, and they will want to put their health first. And in many cases, the work itself is simply too strenuous for a portion of your potential workforce. Without the arm, you’re limiting your hiring pool at a time when the labor shortage is a top concern across industries. With the arm, you can open up roles to a broader pool and improve conditions for existing employees.
Bottom Line: Not using a torque arm can mean you’re at risk of several financial consequences. If employees are injured, there are costs associated with their care and absence. If a tool is dropped and needs repair or is totally out of service, you’ll have to pay out. And if your production quality isn’t up to snuff, you’ll spend time correcting each quality issue and may end up with hits to your reputation.
Examples of Torque Reaction Arms in Action
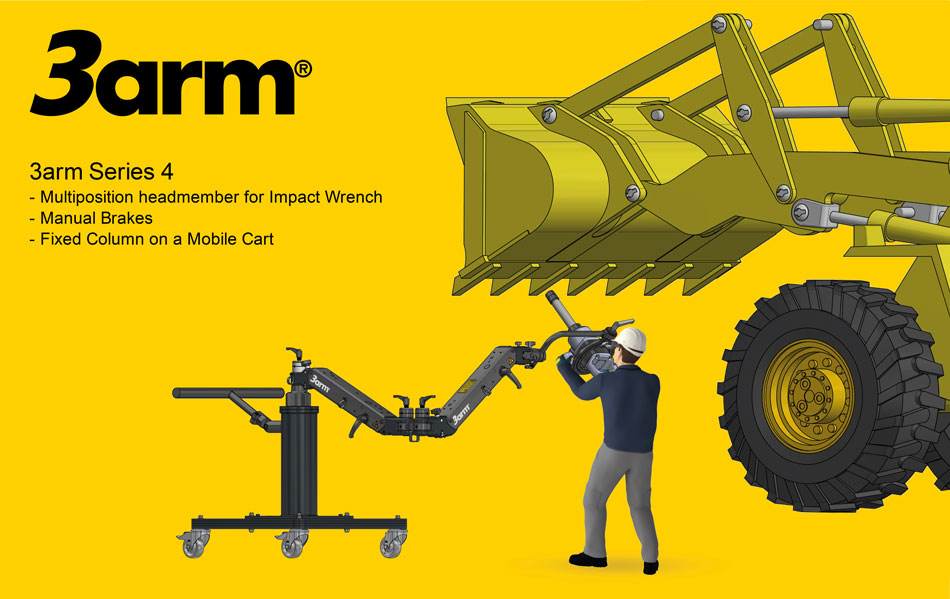
Agricultural Machining Application for 3arm Torque Arm
An agricultural machining manufacturer solved for torque reaction injuries related to fastening bolts to heavy vehicles. The torque force for the application ran up to 200 Nm. The teams at 3arm and partner Rhino Tool House worked with them to design a solution involving a rolling cart system and a 6’ long 3arm tool balancer. With this, they’re able to move the solution from station to station, the tool is weightless and the operator is relieved of the torque force.
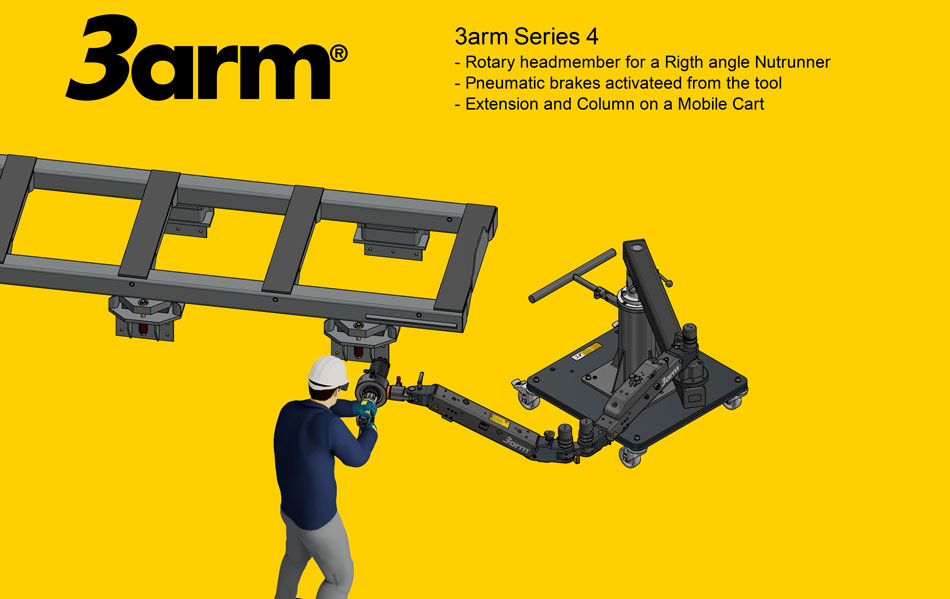
Aircraft Carrier Catapult Application for 3arm Torque Arm
A defense contractor responsible for rebuilding and maintaining catapults for U.S. Navy aircraft carriers needed a mobile torque absorption arm that enabled operators to easily work and maneuver on a busy flight deck. These heavy-duty catapults are used to launch fighter jets off a short deck at a high rate of speed and their maintenance is critical. The team at 3arm developed a trolley and tool-holder system allowing flight deck crews to safely tighten the lug nuts holding the pistons that power the catapult.
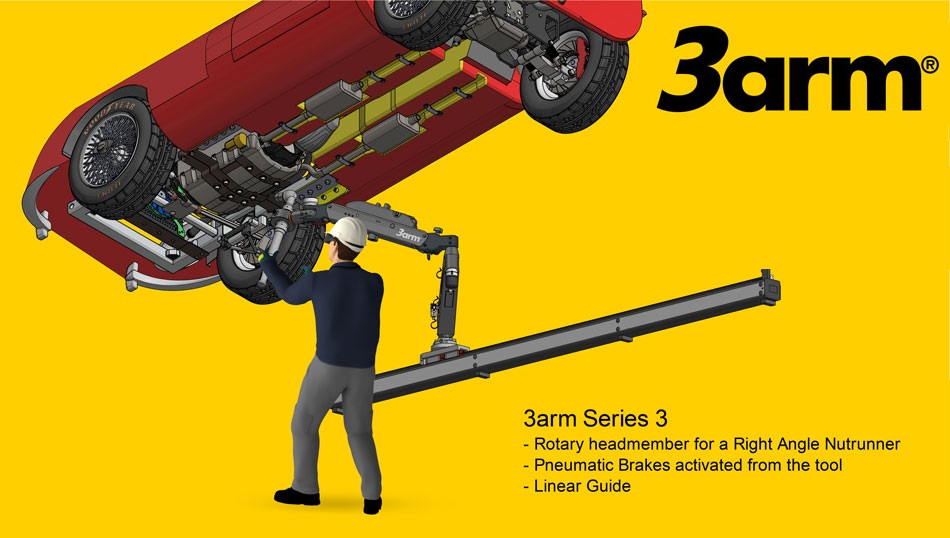
Automotive Underbody Application for 3arm Torque Arm
Automotive manufacturers can implement a 3arm torque arm for underbody shot work, which is taxing work when done manually. The employee must hold a heavy tool at or above shoulder level for extended periods, hold otherwise uncomfortable positions and absorb torque. A torque arm can take the weight off the operator and absorb that torque instead. The arm can also ensure greater consistency and accuracy. Further, the way you design your solution can improve the overall ergonomics of the work. For example, JLC Industrial helped engineers at an automotive assembly plant better plan the assembly line process with precise movements and consistent timing with 3arm tool-holders, providing operators much more control over manual tasks and improves efficiency and, therefore, takt time.
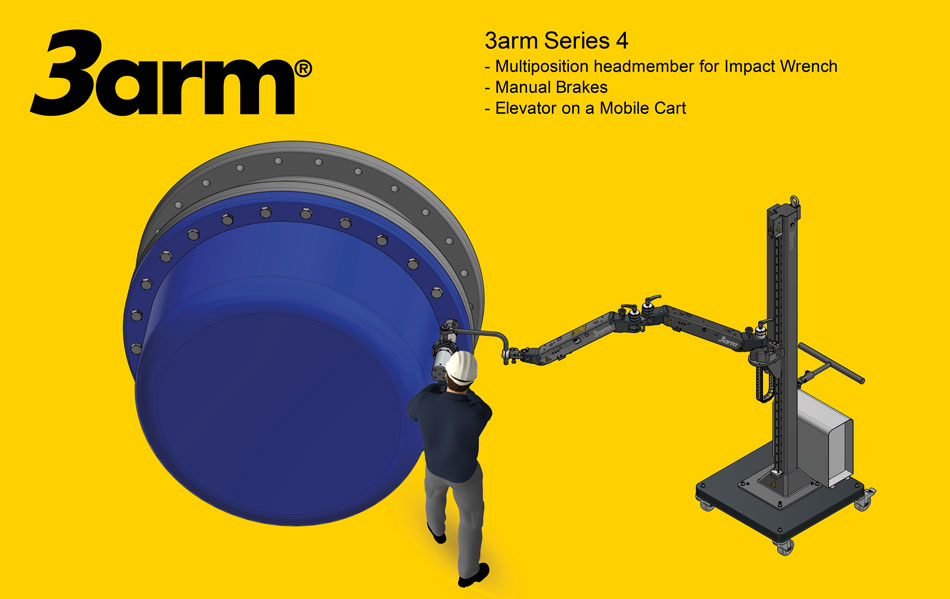
Auger Replacement Application for 3arm Torque Arm
A large manufacturer of tree nut oils used in the food and cosmetic industries needed a way for their operators to safely change several sizes of large augers used in production. This entailed the labor intensive removal and replacement of large bolts with an impact wrench. To keep operators safe from fatigue and possible injuries, the manufacturer ordered a 3arm tool-holder mounted on a trolley which the operators could wheel over to the grinding machine and safely tighten and untighten these bolts to switch augers.

Drilling Application for 3arm Torque Arm
When an operator works with a hand drill for most of the day, the torque reaction and vibration can be the cause of accidents and long term health problems. Hand drills have been known to break an operator’s wrist. Using a 3arm tool-holder with one of 3arm’s many head members prevents injuries as the drill is prevented from transferring torque reaction and vibration forces to the operator.
Are torque arms necessary at your facility? Reach out to us at 3arm America to discuss your application and how our ergonomic torque arms can improve your operations.