How do you know it’s time to invest in an industrial lift assist arm, also known as a zero gravity arm or manipulator?
The signs will be obvious – once you look closely.
You’ll find them on a stroll around the shop floor, in day-to-day conversations, and in your human resources and worker’s compensation files. And when you identify these signs, you’ll also discover all the ways they’re getting in the way of productivity, safety and employee job satisfaction. It’ll be clear how much of an impact one ergonomic arm can have.
You have a range of options when it comes to ergonomic manipulators and lift assist devices for manufacturing. The right option for you will depend on your operations and the signs you see.
Industrial Manipulator Arms
Pick-and-place manipulator arms are used to grip, move and orient parts and objects in your facility. The 3arm Manipulator can handle up to 110 lbs and relieve operators of the need to handle and position heavy, cumbersome parts.
Lift Assist Arms for Tool-Holding and Part-Holding
A tool-holding arm can hold tools, instruments and parts that weigh up to 132 lbs. 3arm’s tool-holding solutions do more than handle the tool – they also absorb torque and reaction forces. They come in a range of options from the Series 0 Single Tilting Arm to the Series 7 Super Duty Arm.
Learn more about the differences between tool-holding and manipulator arms. >>
So, of all the possible investments you could make this year, how do you know it’s time for a 3arm solution? Look for these signs on your shop floor:
1. Employees are experiencing strain and fatigue.
Of course, work is work. But your employees shouldn’t experience constant strain and fatigue. After all, fatigue comes before injury.
Operators should be able to perform their duties comfortably and safely. If they’re complaining of strain and fatigue, and if they must take frequent breaks to prevent over-exertion, you should assess their working conditions.
- Do they have to hold and handle very heavy tools?
- Is constant tool gripping leading to strain?
- Does the vibration or torque of a task hurt their hands?
- Do they frequently move heavy parts from one place to another?
In such instances, a 3arm solution can eliminate issues with strain and fatigue.
For example, a heavy-duty vehicle service technician might work with an impact tool that weighs upwards of 60 lbs for many hours a day. An ergonomic tool holder like the Series 7 arm by 3arm America can carry not only the weight of that tool, but also absorbs up to 1200 ft lbs of torque.
For another example, operators in aerospace and defense industry CNC machining centers are often tasked with lifting heavy parts and transferring tool holders, which could lead to fatigue and injury. In some cases, operators may strip the magazine of 50-100 tool holders for a new job, then load them onto a cart. One tool holder could weigh up to 45 pounds. A 3arm Manipulator can instead take the weight of the part, picking and placing it and relieving the operator of strenuous activity.
Learn how 3arm solutions help you maintain safe limits of force exertion. >>
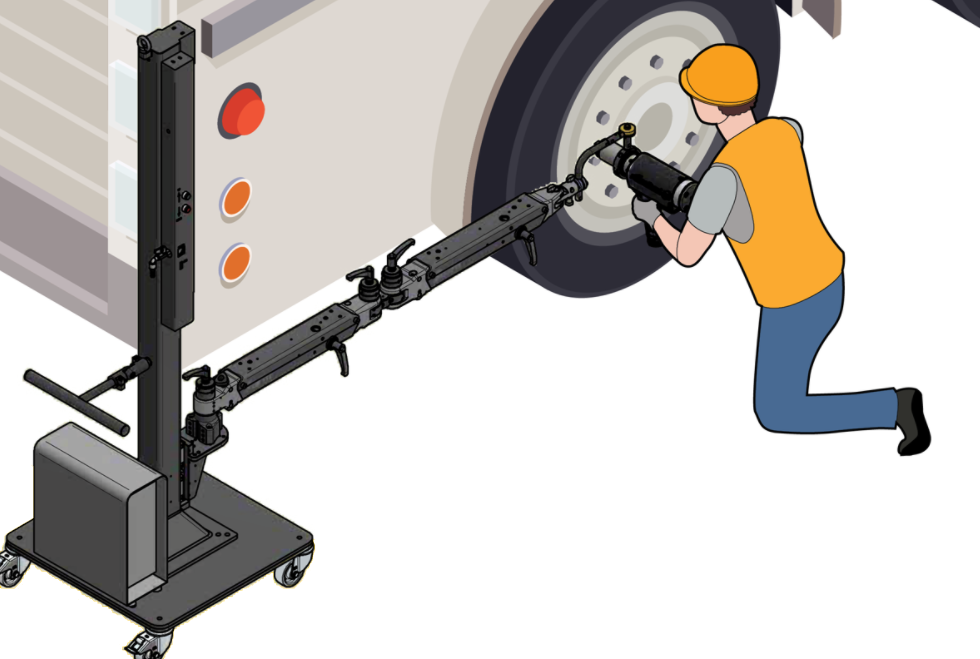
2. Employees are getting injured.
If your operators are developing ergonomic injuries over time or getting sudden injuries performing tasks in your facility, it’s in everyone’s best interest to evaluate your operations and equipment. That’s especially if you’ve had enough worker’s compensation claims to warrant calls from OSHA.
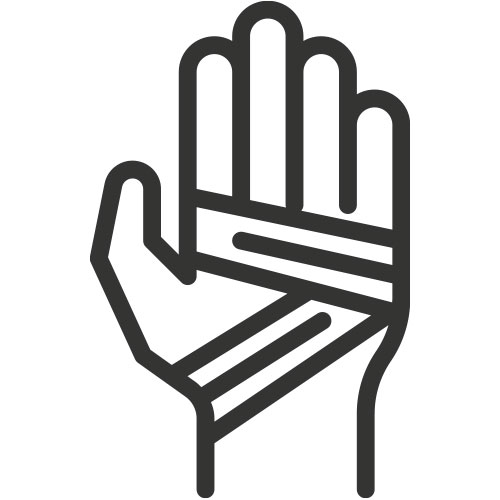
Has an employee developed carpal tunnel? Daily work activities could lead to this syndrome, such as constant use of a heavy impact driver. One carpal tunnel injury can lead to over $65,000 in direct and indirect costs.
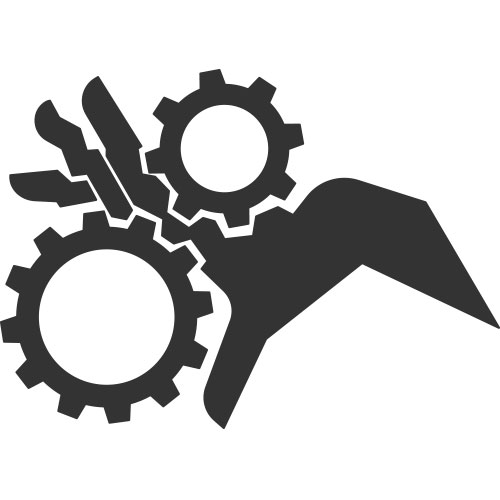
Are employees incurring injuries from pinch zones? Anyone in manufacturing will tell you “pinch zone” is a deceptively mild term considering the range and severity of injuries that could result from getting pinched.

Has an operator broken a bone or bones? For instance, has an operator had their wrist broken due to torque while using a hand drill? This is a clear sign you need to relieve operators of that torque absorption.
There is nothing to lose when you invest in employee safety, and everything to gain. Not only do you show your employees you care about their well-being, but you also avoid the costly ramifications of workplace injuries.
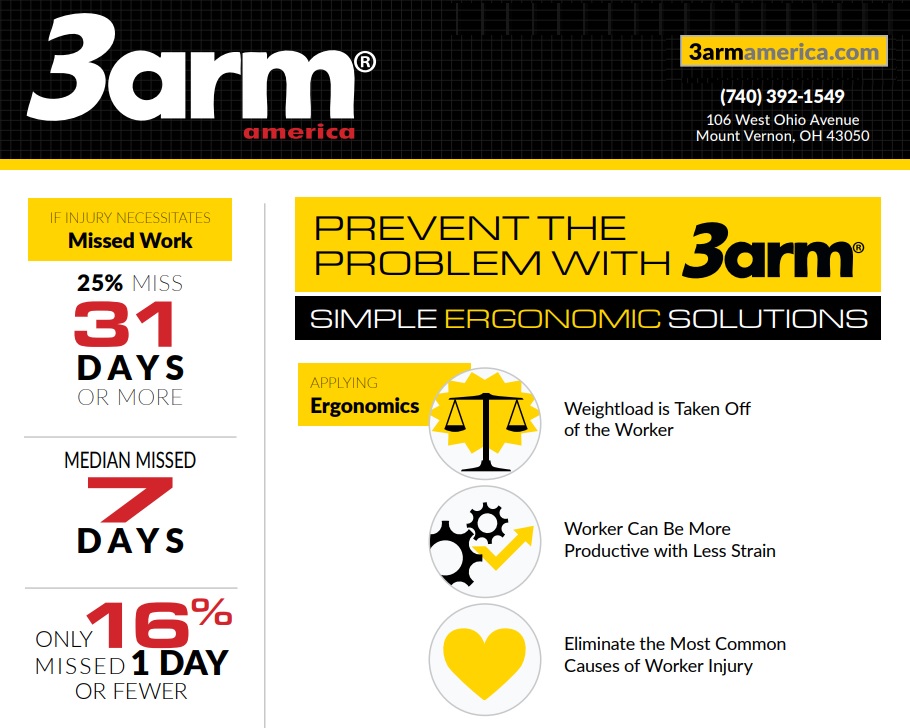
Solutions from 3arm America can resolve issues that lead to injury in your facility. They have no pinch zones, absorb dangerous torque and vibrations, and alleviate the strain of daily duties that lead to ergonomic injuries like carpal tunnel.
For example, the Series 7 has critical safety features that ensure operators’ hands aren’t near pinch point hazards. And the Series 4 tool-holding arm by 3arm America can absorb up to 300 ft lbs of torque. It’s a great fit for heavy-duty fleet maintenance work like removing and replacing truck and bus tires.
3. You have lift or tool-holding tasks that require multiple employees.
If you don’t already use a manipulator or tool-holding arm at your facility, when you analyze your operations, you’ll likely notice several areas where multiple employees are performing tasks that can be consolidated to one operator and an arm.
This isn’t about reducing your workforce. It’s about being more efficient, improving safety and optimizing employee productivity. Manufacturers are dealing with a crippling labor shortage. It’s hard enough getting enough employees to do the work at hand – let alone grow your business. Using 3arm solutions to optimize tasks means operators can spread out to perform other tasks.
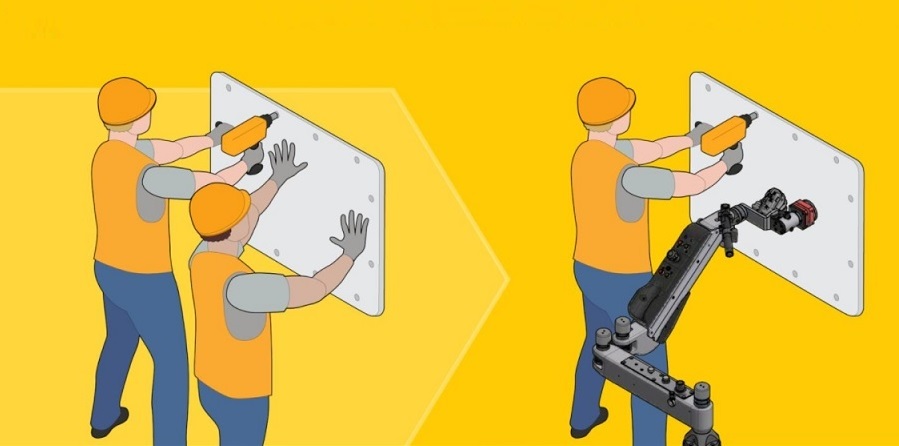
For example, a 3arm manipulator can be used to hold and position heavy parts in place while fastening or changing out tool-holders in a CNC machine. There are numerous safety benefits to using a 3arm solution in your manufacturing facilities.
4. You have heavy-duty tasks and jobs few employees can perform.
If you rely on one or two specific individuals to perform heavy-duty lifting tasks or tool-holding, your production processes depend on them being available. An example of this would be if a task requires a specific height or strength. If your go-to operators for this task are sick or on vacation, does production stop? And if you need to hire for this position, you’ll have a limited pool of prospects.
Today, manufacturers are looking for ways to make their operations amenable to a broader, more diverse pool of employees. If you can optimize a task so that more people can perform it, you can reduce risk in your operations and diversify your workforce. 3arm solutions are perfect solutions, as they lift the weight off the operator and allow one person to do the work of two or more.
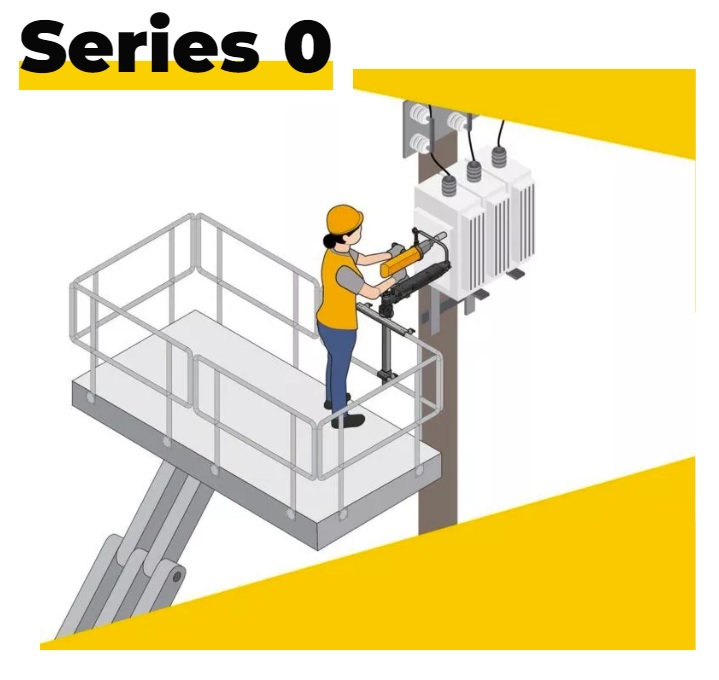
For example, we helped a major paint manufacturer optimize a process that required specific height and strength. Before 3arm, their operator had to fill several 500-gallon totes with a polymer by standing on a foot stool and holding a flexible hose over their head for 10 minutes, directing the hose nozzle into the opening in the tote. We worked with them to design a solution using a Series 3 lift assist arm, a multi-position articulated head member (T) and a trolley with an elevator and locking wheels. The T-head member gives them rotation for positioning the nozzle, incredibly helpful given the heavy weight of the substance in the hose. And now they can lift the trolley as high as it needs to be, walk away and let it drain. Then, they can take it out and move it to the next tote.
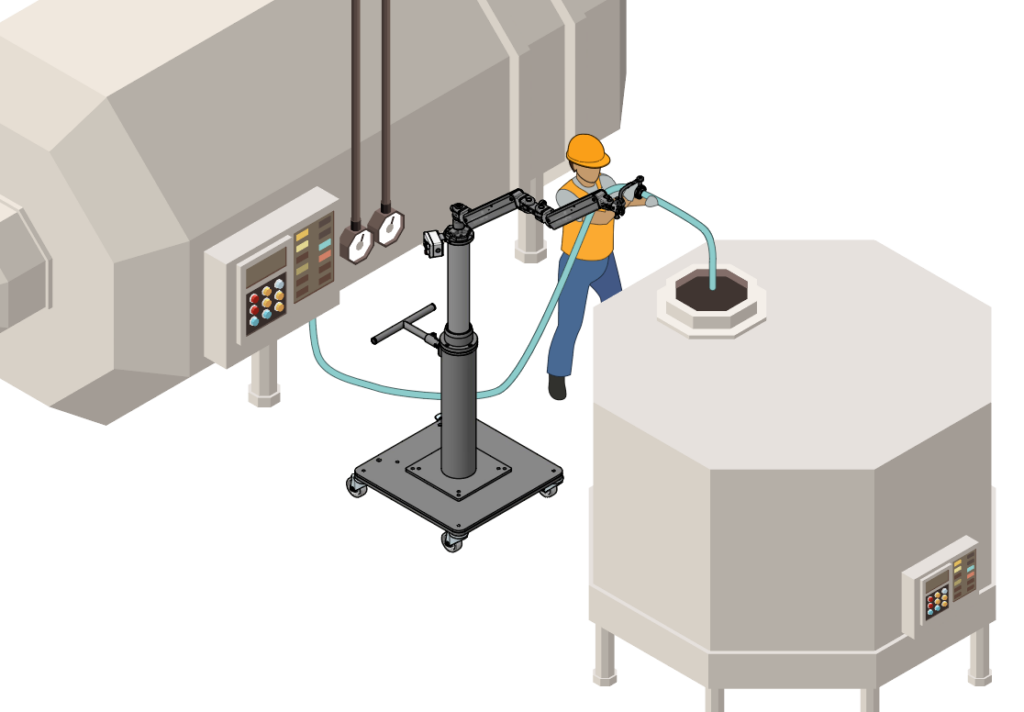
5. You’re constantly reworking parts.
If you’re frequently sending parts back to be reworked because they aren’t passing inspection, you’re likely dealing with consistency and accuracy issues. There are many possible reasons for this, and in many cases, it comes down to the challenge of being consistent with manual tasks that require exertion. Different people apply different levels of pressure and handle loads in their own way. If you can relieve operators of elements of exertion and weight so they can focus on accuracy, you can achieve greater consistency and quality.
For example, a manufacturer may use paint rollers to apply a substance to a surface. Each employee in this case will likely roll with varying pressure. To improve consistency, the manufacturer can implement an ergonomic arm with the paint roller to maintain a uniform pressure.

6. You’re constantly scrapping parts – and repairing tools.
Handling heavy tools and cumbersome parts can lead to damage – every single day.
- Tools and parts could be dropped.
- The operator may remove too much material due to the weight of the tool.
- The tool may make too much contact with the part, damaging it.
If you find you’re sending a lot of parts to the trash heap or tools for repair, consider the benefit of letting a secure lift assist device or tool-holding arm carry the burden. Scrap aside, tools for manufacturing applications are expensive. For instance, a nut runner can be a four-digit expense – not including the control unit. If this tool gets dropped a few times, it’ll likely need a costly repair or be out for the count.
Check out the three critical production assets you can protect with 3arm. >>
How can a lift assist device help? Let’s say your application requires an operator use a grinder at a 90-degree angle. It’s challenging to wield a heavy tool at this angle and achieve the desired result, time after time. There’s a risk the operator will take off too much material or damage the part or tool. And to harken back to another sign, it’s not a comfortable position for the operator.
With a 3arm tool-holder, the process is weightless, more comfortable and more accurate. The arm holds the grinder, taking the weight off the operator and keeping the tool from hitting the workpiece too much. It gives the operator greater control, relieves them of strain, requires less movement per part and allows for precision.
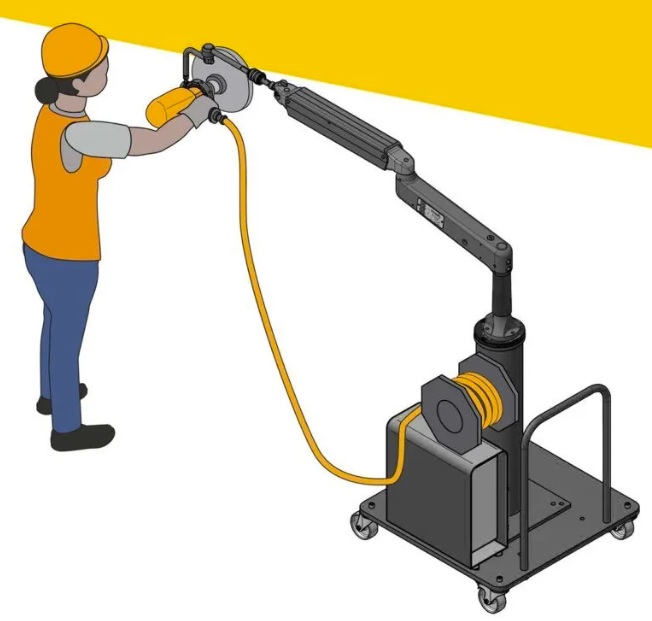
The Manipulator can also be used to handle cumbersome parts. For example, aerospace manufacturers can use the Manipulator to handle heavy, awkward turbine blades so operators don’t have to worry about dropping them or getting nicked by the sharp blades.
7. Employees are leaving and recruits aren’t biting.
It’s not unheard of for operators and other employees to leave a job due to the strain of the work. Handling heavy tools and parts day after day takes a physical and mental toll. Your existing employees may leave if the work is too arduous to be done unassisted. And that arduous work won’t be attractive to potential new hires either.
With 3arm, you broaden your hiring pool and make your roles more attractive to prospective hires. Practically anyone can work with 3arm solutions, and they won’t struggle with consistency or safety. You’ll also be protecting your current employees and showing them how much you care for their health and well-being.
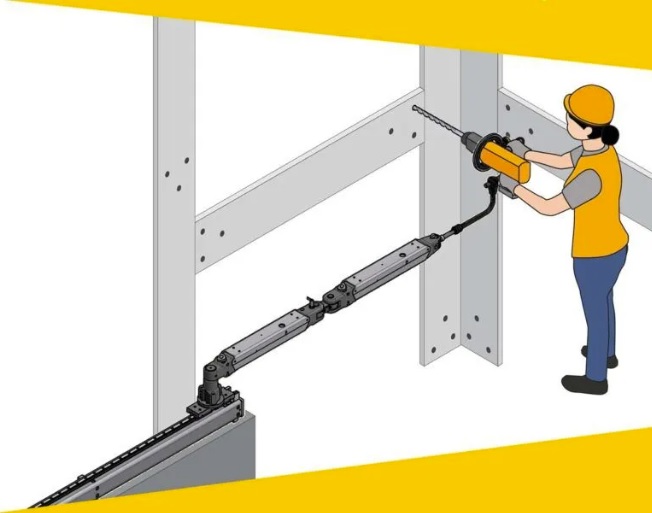
Learn why a safer workplace is essential in attracting and retaining manufacturing employees. >>
Have you observed any of these signs at your facility? Reach out to us at 3arm America to learn more about our solutions and how they can enhance your operations.